More About Alcast Company
More About Alcast Company
Blog Article
The smart Trick of Alcast Company That Nobody is Talking About
Table of ContentsNot known Facts About Alcast CompanyThe Of Alcast CompanyThe 15-Second Trick For Alcast CompanyAlcast Company - TruthsSome Known Details About Alcast Company The Greatest Guide To Alcast Company
The subtle difference depends on the chemical content. Chemical Comparison of Cast Aluminum Alloys Silicon advertises castability by reducing the alloy's melting temperature level and boosting fluidity during casting. It plays a vital function in allowing elaborate mold and mildews to be filled accurately. In addition, silicon adds to the alloy's stamina and use resistance, making it important in applications where longevity is crucial, such as vehicle components and engine elements.It likewise improves the machinability of the alloy, making it less complicated to process into finished items. This way, iron contributes to the total workability of aluminum alloys. Copper enhances electrical conductivity, making it beneficial in electrical applications. It likewise enhances rust resistance and includes in the alloy's total toughness.
Manganese adds to the strength of aluminum alloys and boosts workability (Casting Foundry). It is typically utilized in functioned aluminum items like sheets, extrusions, and profiles. The visibility of manganese help in the alloy's formability and resistance to splitting during construction processes. Magnesium is a light-weight aspect that offers strength and effect resistance to aluminum alloys.
Alcast Company for Beginners
It permits the manufacturing of lightweight components with outstanding mechanical buildings. Zinc enhances the castability of aluminum alloys and assists regulate the solidification process throughout spreading. It boosts the alloy's toughness and solidity. It is usually located in applications where elaborate shapes and fine details are necessary, such as decorative castings and specific automobile components.
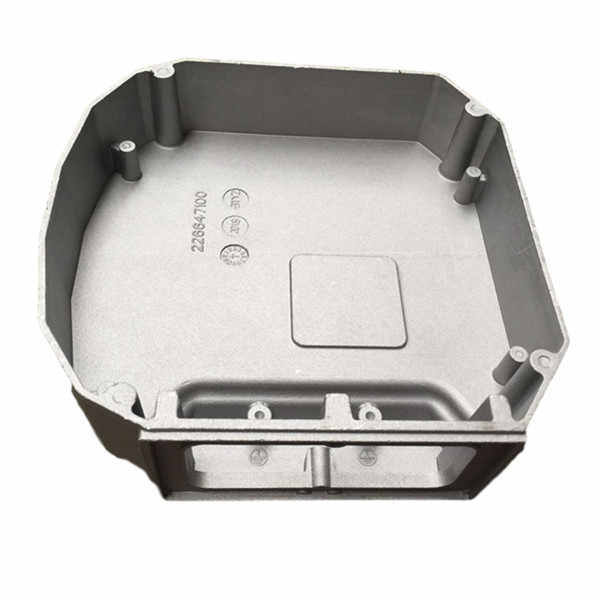
The key thermal conductivity, tensile toughness, yield toughness, and elongation differ. Select ideal raw products according to the efficiency of the target product produced. Among the above alloys, A356 has the highest possible thermal conductivity, and A380 and ADC12 have the least expensive. The tensile restriction is the contrary. A360 has the very best return strength and the highest possible prolongation rate.
Getting The Alcast Company To Work
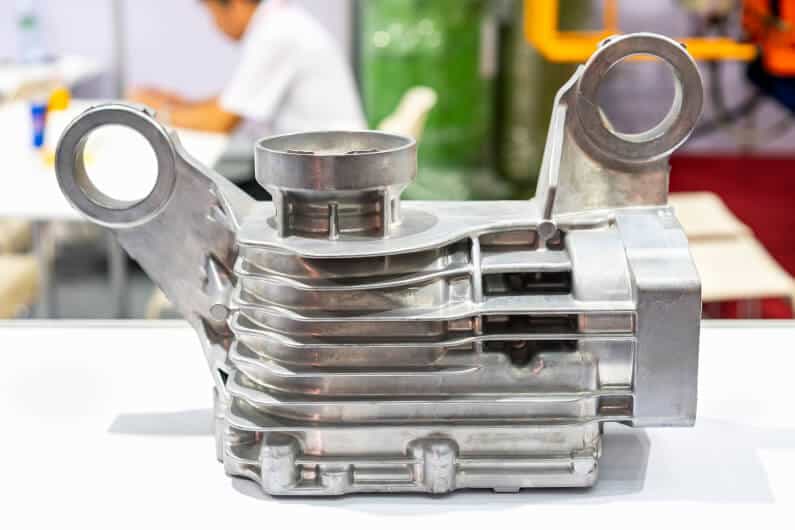
Its one-of-a-kind residential or commercial properties make A360 a valuable choice for accuracy casting in these industries, enhancing item sturdiness and high quality. Aluminum Castings. Aluminum alloy 380, or A380, is a widely used spreading alloy with numerous distinctive features.
In precision spreading, aluminum 413 radiates in the Customer Electronic Devices and Power Tools industries. This alloy's exceptional corrosion resistance makes it an outstanding choice for exterior applications, ensuring long-lasting, sturdy products in the mentioned industries.
Our Alcast Company PDFs
As soon as you have decided that the light weight aluminum die casting process is suitable for your job, a crucial next step is choosing one of the most suitable alloy. The aluminum alloy you pick will substantially affect both the casting procedure and the buildings of the last item. Due to this, you have to make your decision very carefully and take an enlightened approach.
Figuring out the most appropriate light weight aluminum alloy for your application will indicate considering a wide range of qualities. The first category addresses alloy features that influence the manufacturing procedure.
Unknown Facts About Alcast Company
The alloy you pick for die casting straight impacts several facets of the spreading procedure, like how simple the alloy is to collaborate with and if it is vulnerable to casting defects. Warm cracking, additionally called solidification breaking, is a regular die spreading defect for light weight aluminum alloys that can cause internal or surface-level splits or cracks.
Specific aluminum alloys are more at risk to hot breaking than others, and your choice needs to consider this. One more typical issue located in the die spreading of light weight aluminum is die soldering, which is when the cast stays with the die walls and makes ejection tough. It can harm both the actors and the die, so you ought to look for alloys with high anti-soldering properties.
Corrosion resistance, which is currently a noteworthy feature visit here of aluminum, can vary significantly from alloy to alloy and is a necessary particular to take into consideration relying on the environmental conditions your item will be exposed to (aluminum casting manufacturer). Wear resistance is an additional residential property commonly sought in light weight aluminum products and can set apart some alloys
Report this page